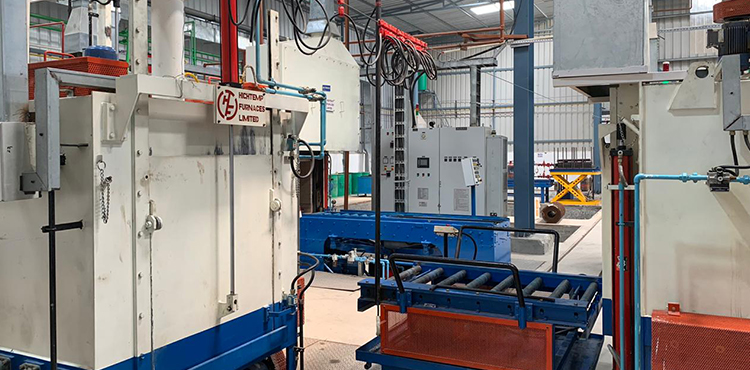
Heat Treatment
At INSCO we have installed a heat treatment, High-strength or heat-treated fasteners are often required to handle the tensile, shear or combination loads on the bolted joints in demanding applications. Many demanding applications require high-strength fasteners in order to handle high tensile and shear stresses generated by the applied loads on the bolted or fastened joint.
HIGH-STRENGTH OR HEAT-TREATED FASTENERS
Oil and gas, petrochemical, chemical and power generation plants contain boilers, pressure piping vessels, valves and process equipment requiring high-strength bolting to maintain seal closure on flanged joints, fittings and closures. Heat-treated bolts are needed to withstand the tensile stresses within the bolts. High horsepower industrial mixers and pump drive shafts often require the higher shear strength provided by heat-treated bolts or pins.
Building and construction anchor bolts such as J-bolts, L-bolts or drop-in wedge anchors, attach equipment or structural members to concrete pads or foundations. Structural anchor bolts are made of carbon or fully heat-treated medium alloy steel.
About 90 percent of fasteners are steel based and the required strength level is usually developed in steel fasteners using quenching and tempering processes. Accordingly, the terms “high strength” with “heat treated” or “hardened” are often equivocated with the fastener world. However, heat treatment includes a wide range of processes. Some heat treatments like annealing soften a metal, while others harden and strengthen. Annealing heat treatments are used to relieve residual stress, remove cold work and dissolve the alloying element or segregation and provide a more homogeneous material.
Higher carbon steels can be hardened, while low carbon steels are considered non-hardenable. The steel in low-strength ASTM A307 or SAE Grade 2 fasteners is a low carbon grade, such as AISI 1018 or 1020. Grade 304 or 316 austenitic stainless steel fasteners contain little carbon and therefore cannot be hardened by heat treatment. Certain martensitic stainless grades, such as ASTM A193 grades B6 and B5, can be hardened through a quench and temper heat treatment. Grades B5 and B6 are used in high-temperature and high-pressure service and special purpose applications. Heat treatments of stainless bolts are employed to dissolve coarse chromium carbide particles, which may reduce corrosion resistance and toughness. The carbide solution treatment of stainless steel fasteners can improve cryogenic or low temperature toughness and is part of the ASTM A320 specification. ASTM A325, ASTM A490 SAE grade 5 and SAE grade 8 fasteners are made of higher carbon plain or alloy steels, which can be hardened through a quenching and tempering process. Heat treated SAE grade 8 bolts have twice the minimum tensile strength of SAE grade 2 bolts.
QUENCH & TEMPER HARDENING PROCESS
In the quench and temper hardening process, steel fasteners are first heated up to a temperature where their structure is converted into austenite and then quenched or rapidly cooled in water, oil or air to crystal structures that transform to martensite. Next, the martensitic steel fasteners are heated at an intermediate tempering temperature to change the martensite to ferrite, with a very fine dispersion of cementite. Steels cooled slowly from austenitizing temperatures, as well as nonhardenable, low carbon grade steels, form a softer, coarser pearlite structure of ferrite and iron carbides (cementite). The cooling rate has to be fast enough to avoid the formation of pearlite.
DEGREES OF HARDENABILITY
Even among hardenable steels, the degree of hardenability varies with level of carbon and alloying elements like chromium, molybdenum, manganese, silicon, vanadium and nickel, which retard ferrite formation and shift the nose of pearlite to start formation of the curve to the right (Figure 4). The hardenability impacts how deeply into the material the hardness changes will occur during the heat treatment process. Steel alloys with higher carbon and alloying elements can be through hardened and transformations will occur throughout the part even at lower cooling rates, which reduces residual stress and distortion during heat treatment. In lower hardenability alloys, hardening will only occur part way into the alloy from the surface.
PROPER USE AND MAINTENANCE OF HARDENED STEEL FASTENERS
While high-strength steel fasteners are a critical element and an enabler in many advanced structure and high tech mechanical designs, care needs to be taken in using hardened steel fasteners. High-strength fasteners with a Rockwell C hardness above 35 are susceptible to hydrogen embrittlement. Hydrogen embrittlement causes a loss or partial loss of ductility in hardened steel, which can result in sudden, catastrophic and premature failures of the fastener in the field. Exposure to hydrogen during processing or in the field application should be avoided. Atomic hydrogen can be absorbed into steel fasteners during phosphating, pickling (acid cleaning or descaling), plating and electrogalvanizing processes. While alternate protective coatings are recommended, a hydrogen bake heat treatment can be used to remove residual hydrogen after plating or electrochemical processes.
For the safety and proper working for the stud bolts we at INSCO have installed a sealed quench furnace from DOWA Japan. This is the first of its kind heat treatment set up in Middle east