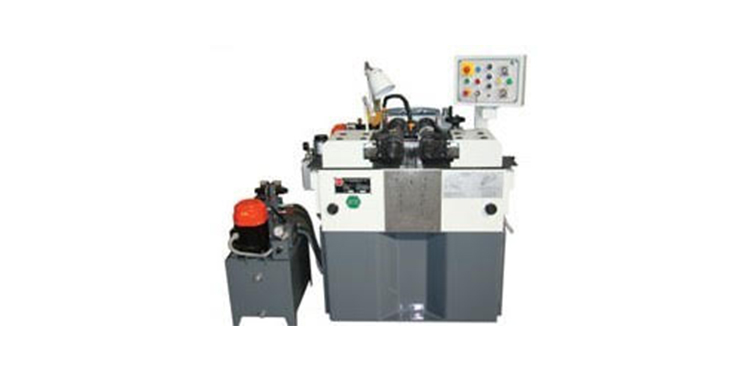
Thread Rolling
Screw threads may be formed by rolling either by using some type of thread rolling machine or by equipping an automatic screw machine or turret lathe with a suitable threading roll. If a thread rolling machine is used, the unthreaded screw, bolt, or other “blank” is placed (either automatically or by hand) between dies having thread-shaped ridges that sink into the blank, and by displacing the metal, form a thread of the required shape and pitch. The thread-rolling process is applied where bolts, screws, studs, threaded rods, etc., are required in large quantities. Screw threads that are within the range of the rolling process may be produced more rapidly by this method than in any other way. Because of the cold-working action of the dies, the rolled thread is 10 to 20 percent stronger than a cut or ground thread, and the increase may be much higher for fatigue resistance. Other advantages of the rolling process are that no stock is wasted in forming the thread, and the surface of a rolled thread is harder than that of a cut thread, thus increasing wear resistance.