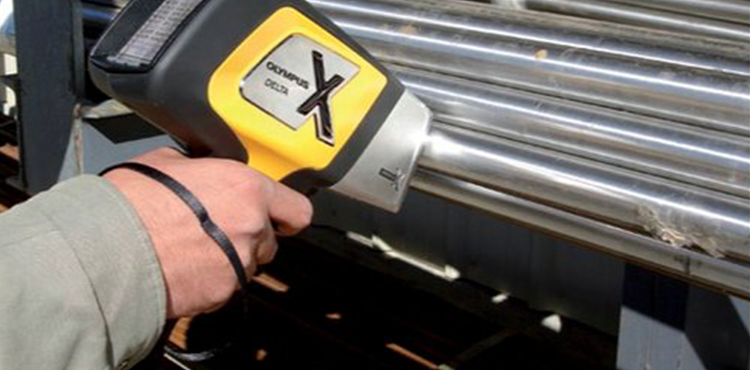
Non-Destructive Testing
The process of inspecting testing and evaluating components for differences in characteristics without destroying the serviceability of the part or system. NDT techniques are used to detect service related conditions caused by wear, fatigue, corrosion, stress or other factors that affect reliability.
Ultrasonic Testing (UT)
At INSCO fasteners we offer ultrasonic testing, high frequency sound waves are introduced into a material via an ultrasonic transducer connected to a UT gauge coupled to the test object by couplet to detect imperfections. There are two methods of receiving the ultrasound waveform, reflection and attenuation. The most widely used technique reflection (or pulse-echo) mode, whereby sound is introduced into a test specimen and reflections (the echoes) coming from the internal imperfection or the part’s geometrical surfaces such as the back wall of the object are returned to the device.
Magnetic Particle Testing (MPT or MPI)
At INSCO fasteners we also perform Magnetic particle inspection (MPI) which is a non-destructive testing (NDT) process for detecting surface and partially subsurface discontinuities in ferromagnetic material such as iron, nickel, cobalt, and some of their alloys. The process puts a magnetic field into the part.
The presence of a surface or subsurface discontinuity in the material allows the magnetic flux to leak. Dry or wet ferrous iron particles are applied to the part.If an area of flux leakage is present, the particles will be attracted to this area. The particles will build up at the area of leakage and form what is known as an indication. From the Visible indication, the location, size and shape can be assessed.